Compte tenu du rétrécissement et de la déformation de l'engrenage et de la précision non requise du trou de l'arbre d'engrenage lors du moulage par injection de l'engrenage en plastique, la conception optimisée du système de verrouillage, le mécanisme de démoulage et la méthode de refroidissement sont utilisés pour produire le plastique de précision engrenage qui répond aux exigences, améliorant ainsi les performances de l'engrenage. performance.
1. Avec le développement rapide de l'industrie, les gens ont une grande demande d'appareils photo, d'imprimantes et de copieurs dans la vie quotidienne et au bureau. Les engrenages en plastique ont progressivement remplacé les engrenages en métal. Ces équipements ont des exigences relativement élevées pour la précision d'engrènement des engrenages. Dans la conception de la surface de séparation de la pièce en plastique d'engrenage, les inserts en forme de dent avec la même forme de la cavité de moule fixe et la conception de noyau de moule mobile adoptent une disposition de 1 moule et 1 cavité. Afin d'éviter les phénomènes indésirables tels que l'insatisfaction et la déformation du moulage par injection, le moule adopte une méthode d'injection équilibrée à 3 points de porte de moule à trois plaques. Afin de démouler en douceur les pièces en plastique de l'engrenage sans laisser de traces, une broche de berceau ronde est utilisée pour équilibrer. En optimisant la conception de ces trois systèmes, la précision et les performances des engrenages sont garanties.
2 Analyse de processus de pièces en plastique
L'engrenage en plastique est illustré à la figure 1. Le matériau sélectionné est le polyoxyméthylène (POM), qui présente de bonnes propriétés mécaniques, et le taux de retrait au moulage est de 2 % à 3 %. Lorsque la température du matériau est élevée, il change de couleur. Le système de refroidissement doit être conçu. La circulation est uniforme et bonne, et la température du moule d'injection est garantie à 80℃~100℃.
Comme le montre la figure 2, le diamètre extérieur maximal de l'engrenage en plastique est la poulie, basé sur le trou d'arbre central ϕ 4 mm, l'exigence de coaxialité est ϕ 0,05 mm, et la poulie et le trou central 4 mm et la tolérance de forme de faux-rond complet l'exigence est de 0,05 mm. La sélection de la surface de séparation principale est basée sur la surface supérieure ϕ 11 mm de contour maximum, la zone de couleur claire est définie dans la partie de moule fixe, et la zone sombre et l'arbre intermédiaire formant le noyau sont définis dans la partie de moule mobile, qui peut assurer la précision de l'engrenage en plastique. Les caractéristiques avec des tolérances de forme et de position et des tolérances dimensionnelles sont déterminées selon la nuance MT5, et pour les tailles libres, la valeur de tolérance peut être obtenue selon la table de correspondance MT7.
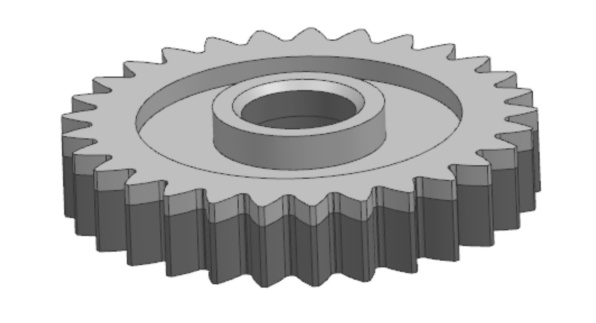
|
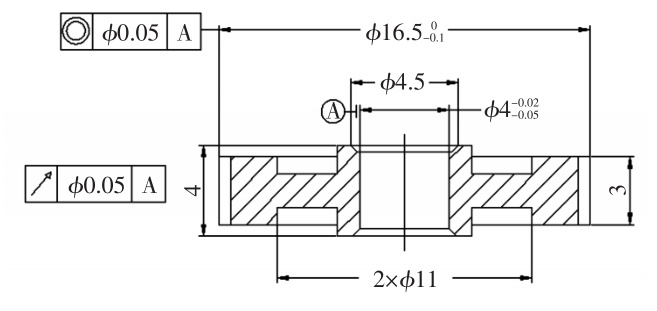
|
3 Conception du système de déclenchement (1) Le diamètre de la petite extrémité du canal principal est ϕ 0,5 ~ ϕ 1 mm en fonction du diamètre de la buse de la machine de moulage par injection, l'angle de cône du canal principal est de 2 ° ~ 6 °, la longueur est 60 mm, et le diamètre de la petite extrémité de la glissière principale de l'engrenage en plastique est ϕ 2,5 mm, l'angle du cône est de 2° et la longueur réelle est de 37 mm. (2) Le coureur adopte une section en forme de U couramment utilisée, H = 1,25 R, R = 0,5 B, et le coureur d'engrenage en plastique H est de 3,0 mm, B est de 3,9 mm et R est de 1,7 mm pour rendre le plastique dans un État fondu. Il s'écoule rapidement dans les canaux et est rempli uniformément, assurant une bonne pression et un remplissage uniforme. (3) Les types de barrières incluent généralement les barrières latérales et les barrières ponctuelles. Les portes latérales ne peuvent être conçues que sur le plan de joint principal. La conception et le traitement sont pratiques, mais il y a des marques de porte. Afin d'obtenir un plastique de haute précision et de haute finition, la méthode de coulée à trois portes est donc sélectionnée. L'avantage de la porte ponctuelle est qu'il n'est pas nécessaire de couper la bavure, la porte tombera automatiquement et une production automatisée peut être réalisée. Le plastique à l'état fondu s'écoule radialement de la porte vers l'environnement et 3 lignes de soudure sont formées à la jonction d'écoulement. Au niveau de la ligne de soudure, le front d'écoulement a tendance à être parallèle, et une zone de faible retrait est formée le long de la ligne de soudure, qui n'est pas facile à déformer, de manière à obtenir des engrenages de haute précision. Pour résumer l'analyse, combinée au logiciel d'analyse de flux de moule MoldFlow pour déterminer le point de coulée, la conception du système de coulée pour engrenages en plastique, comme indiqué sur la figure. 4 Conception du système de refroidissement Lorsque le moule est injecté sur la machine de moulage par injection, le matériau de la pièce en plastique est du POM, qui est un matériau sensible à la chaleur, et il est facile de changer de couleur lorsque la température du matériau est élevée. Par conséquent, afin de contrôler la température du matériau et le temps de moulage pendant le moulage par injection, un système de refroidissement doit être raisonnablement mis en place pour garantir que la température du moule est maintenue entre 80°C et 100°C pendant l'injection. La plaque dévêtisseur est équipée d'un circuit d'eau circulant, et les gabarits fixe et mobile sont pourvus chacun de 2 canaux d'eau symétriques et rectilignes. Le diamètre de la section transversale du canal d'eau est ϕ 8 mm. La conception du système de refroidissement du moule est illustrée à la figure 4. Le gabarit fixe et la surface de la dent sont pourvus de rainures d'échappement. Afin d'éliminer l'air emprisonné, la profondeur de la rainure est inférieure à la valeur de débordement du plastique et la profondeur de la rainure est de 0,2 mm.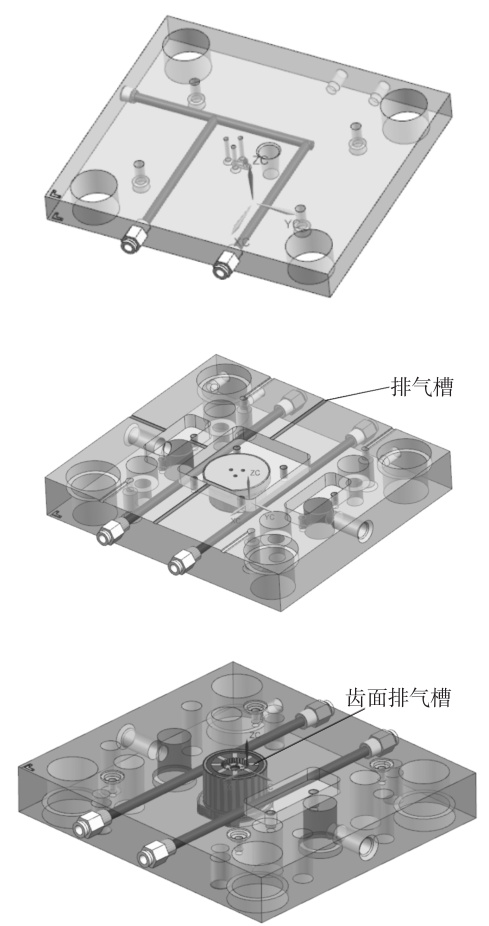
|
6 Lancement de la conception du mécanisme Les mécanismes de poussée couramment utilisés comprennent les tiges d'éjection, les cylindres et les plaques de poussée. La plaque de poussée convient à la coque et aux pièces en plastique qui ne doivent pas laisser de traces sur la surface extérieure. Le cylindre est couramment utilisé pour faire sortir des pièces en plastique cylindriques, en forme d'anneau et percées. Ce type de force de démoulage est uniforme et la pièce en plastique est faible en déformation, mais sa précision est faible. Il peut être utilisé pour les engrenages inférieurs au niveau 4. Il y a un espace au milieu du cylindre, ce qui augmente Introduire l'erreur. La tige d'éjection peut éjecter les pièces en plastique de manière uniforme. Ce type de démoulage peut garantir la tolérance de faux-rond des pièces en plastique et la précision peut atteindre 3 niveaux ou plus. Selon les caractéristiques de la pièce en plastique, la goupille d'éjection est choisie pour sortir, comme le montre la figure 6.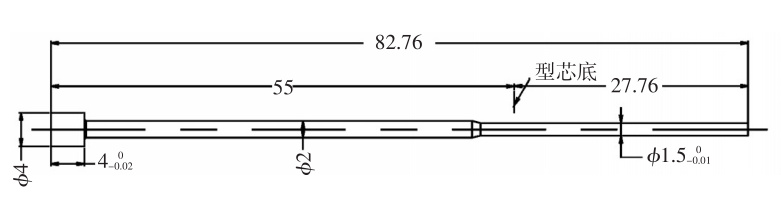
|
7 Structure d'assemblage de moules et son processus de travail La structure de l'ensemble de moule est illustrée sur la figure. Lorsque le moule est ouvert, afin d'éviter que la pièce en plastique d'engrenage ne soit tendue ou laissée sur le côté du moule fixe, un ressort 16 est conçu sur la petite tige de traction pour séparer préférentiellement le plan de joint Ⅰ-Ⅰ du Ⅱ -Ⅱ plan de joint. La grille se désolidarise de la partie plastique de l'engrenage sous l'effort de la tige 19 ; le moule mobile se déplace vers le côté tige supérieure de la machine de moulage par injection. Lorsque le côté gauche du gradin du petit tirant 11 touche le côté droit du gabarit fixe 4, le plan de joint Ⅰ-Ⅰ se déplace Fin ; le plan de joint Ⅱ-Ⅱ est séparé en tant que plan de joint principal. En raison de la force d'emballage de la pièce en plastique d'engrenage, la pièce en plastique reste sur le noyau de moule mobile. La plaque de traction de positionnement sur la face supérieure du moule limite la distance de la surface de séparation Ⅱ-Ⅱ (la distance de séparation de Ⅰ-Ⅰ, Ⅱ-Ⅱ peut permettre à la tête de matériau et aux pièces en plastique d'engrenage de se vider automatiquement); par la suite, la surface de séparation Ⅲ-Ⅲ est séparée et le matériau de grille tombe ; le moule mobile continue de se déplacer vers la droite et la broche d'éjection de la machine de moulage par injection En poussant la plaque inférieure de la tige d'éjection pour se déplacer, la tige d'éjection éjecte la pièce en plastique d'engrenage du noyau de moule mobile, et la pièce en plastique est automatiquement démoulé. Lorsque le moule est fermé, le ressort 13 sur la tige de réarmement 12 réinitialise préférentiellement l'éjecteur et entraîne l'éjecteur 10 pour revenir à l'état initial. Le côté du moule est fermé, et enfin le moule est fermé. 8 remarques de conclusion Le moule adopte une méthode de porte de point de moule à trois plaques pour le coulage, un moule et une cavité, et trois surfaces de séparation sont conçues. L'air est bon et le rétrécissement et la déformation des pièces en plastique de l'engrenage sont résolus. Lors de la conception du mécanisme d'éjection, le plan de joint Ⅰ-Ⅰ est prioritaire sur le plan de joint Ⅱ-Ⅱ. La tige de traction et la plaque de positionnement sont conçues pour limiter la distance d'ouverture du moule. La tige d'éjection est utilisée pour pousser vers l'extérieur pour assurer la tolérance de faux-rond de la pièce en plastique. Précision. Lorsque le moule est réellement produit, le mécanisme du moule est stable et fiable, et la qualité et la précision du produit fabriqué répondent aux exigences d'utilisation.